Sudarshan Dayanidhi*1 , MS, PT, Jonathan Weisz*1 , BS, Linda Junker2 , PT, Åsa Hedberg2 , PhD, Hans Forssberg2 , MD, PhD, Francisco J. Valero-Cuevas1 , PhD
1 University of Southern California, Los Angeles, California, United States of America
2 Karolinska Institute, Stockholm, Sweden
ABSTRACT
Manual dexterity is often greatly affected in people with neurological insults. While traditional clinical evaluations use various methods to quantify hand function, none focus on capturing the full dynamical interactions among fingers. The Strength-Dexterity test is a system that uses the mechanical properties of slender springs to elicit and quantify a person’s ability to dynamically control fingertip forces and movements. Here we extend that work to create a hand-held version that is clinically useful by using miniature load cells. These innovations allow us to measure the time history of forces at the tips of the thumb and the index fingers during compression and hold task. We are now using this method to study the development of manual dexterity across the life span, and in children with cerebral palsy. We propose that, once validated, this metric will prove to be a useful outcome measure for therapy and other clinical interventions.
Keywords:
Dexterity, Outcome Measure, Hand Function, Stroke, Cerebral Palsy, Precision Grip
BACKGROUND
Dexterous manipulation is a defining characteristic of human function. Following insults to the brain such as stroke or cerebral palsy, this ability can be greatly affected. Most clinical evaluations of hand function focus on strength requirements (such as testing with a pinch meter), sensory tests, functional tasks and questionnaires of functional abilities [(1), (2)]. Many of the functional tests are based on time and the ability to lift objects of various shapes, which—while assessing various sensory or motor components—do not necessarily provide a clear understanding of the dynamic sensorimotor interactions that produce the dexterous abilities of a person. The focus of existing tests arises largely from the limitations of current technology that to this point has not been developed to specifically measure multifinger interactions during dynamical tasks involving the control of individuated finger forces and motions. For these reasons most instrumented tests rely on measurements of static forces during manipulation of rigid objects. The Strength-Dexterity paradigm, in contrast, is a system that uses the mechanical properties of slender springs to elicit and quantify a person’s ability to dynamically control fingertip forces and movements. [(3),(4)]. The control of fingertip forces and motions is a cornerstone of dexterous manipulation [(3)]. In this paper we extend this novel method with miniaturized instrumentation that allows real-time measurements in hand-held devices.
METHODOLOGY:
Instrumentation
We designed housings to mount miniature 1-axis compression 5lb load cells (LBS-5, Interface Inc., Scottsdale, AZ) on the ends of slender compression springs (Figure 1). In our first prototype, the spring specifications are: free length= 39.7mm, wire diameter= 0.5 mm, rate=0.09 N/mm, total coils= 12.5, material= music wire (# 4268, Century Springs Corp., Los Angeles, CA). When compressed, this spring is initially stable, but as the compression increases to a critical point the combined hand-spring system becomes unstable and relies on the anatomy of the hand and the sensorimotor control of the fingers to dynamically hold that level of compression force [(4)]. The housings were printed using ABS plastic with a Dimension Elite 3-D printer (Eden Praire, MN). The compression of this spring involve low forces (2-3 N), but require careful collaborative control of finger motions and fingertip force vectors to prevent the spring from buckling. The sensors were connected to a signal-conditioning box, and a 13- bit USB Data Acquisition card (USB 1408-FS, Measurement Computing, Norton, MA) interfaced with a computer. A custom-written program in MATLAB (Natick, MA) collected the force data at 400 Hz, and a low pass filter (4th order Butterworth at 25 Hz maintaining phase in MATLAB, filtfilt function in Signal Processing Toolbox) removed spurious high-frequency noise. In addition, a 6-axis load cell (Nano17, ATI Industrial Automation, Apex, NC) was used to validate the signals from the 1-axis load cells as mounted on the springs.
Procedures
For the validation task, the spring with a single 1-axis load cell was mounted on top of the 6-axis load cell, and a consenting adult male volunteer compressed and held the spring at a stable point. To demonstrate the use of the device, the subject was asked to compress the device with a precision grip to the edge of instability and hold that level of precision grasp force (Figure2). The University of Southern California institutional review board authorized all protocols.
RESULTS
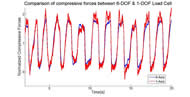
a) Cyclical Loading
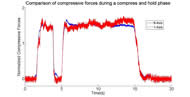
b) Compress and Hold (Click for larger view)
The compression forces between the 1-axis and the 6-axis load cells were compared after normalizing with their respective means and the 1-axis load cell is seen to be fairly representative of the 6-axis load cell (Figure 3).
Importantly, in this dynamical situation we can see that the forces from both fingers need not be equal and opposite, as is the case of static grasp. The mean maximal compression forces generated by the thumb were 1.75 (±0.16) N while those from the index finger were 2.15 (±0.09) N (Figure 4). This is the rule in dynamical systems where the imbalance of forces interacts with gravity and the inertia, stiffness and viscosity of the system to produce time-varying kinematics.
DISCUSSION
In this paper we illustrate radical improvements in our method for capturing a dexterity metric to make it clinically useful. We have extended our previous work to a portable, hand-held system which can record high-resolution force data from the fingertips in a clinical setting. Of primary concern was to validate whether the housing we use to mount the one-dimensional load cells did not pollute the force signal. Our validations against a high-resolution three-dimensional load cell show that the miniature one-dimensional load cells do measure the force perpendicular to the finger pad produced by the fingertips. We are now using this method to collect high-resolution time histories of fingertip force in healthy young adults, the elderly, typically developing children and children with cerebral palsy. The limitation remains that we cannot measure the full 3-dimensional fingertip force vector, but that is goal of our future work. Nevertheless, with the miniature sensors and the modifications to the properties of the spring we have developed the first system capable of recording finger forces during dynamic manipulation of unstable objects. We believe this new method will provide critical information for outcome measurement in children with cerebral palsy and adults with stroke, which will be useful for evaluation of efficacy of treatment.
REFERENCES
- Taylor, N., Sand, P.L., Jebsen, R.H. (1973). Evaluation of hand function in children. Archives of Physical Medicine Rehabilitation, 54,129–35.
- Valero-Cuevas, F.J., Smaby, N., Venkadesan, M., Peterson, M., Wright, T. (2003). The strength-dexterity test as a measure of dynamic pinch performance.Journal of Biomechanics, 36, 265-270.
- Van Heest, A.E. (2003). Functional assessment aided by motion laboratory studies. Hand Clinics, 19, 565-571.
- Venkadesan, M., Guckenheimer, J., Valero-Cuevas, F.J. (2007). Manipulating the edge of instability. Journal of Biomechanics, 40,1653-1661.
ACKNOWLEDGEMENTS:
* Both of these authors are considered to have contributed to the project equally. We would like to acknowledge the technical assistance of Cornelius Raths.